Tecon sistem – automatski kranovi za svaku proizvodnju
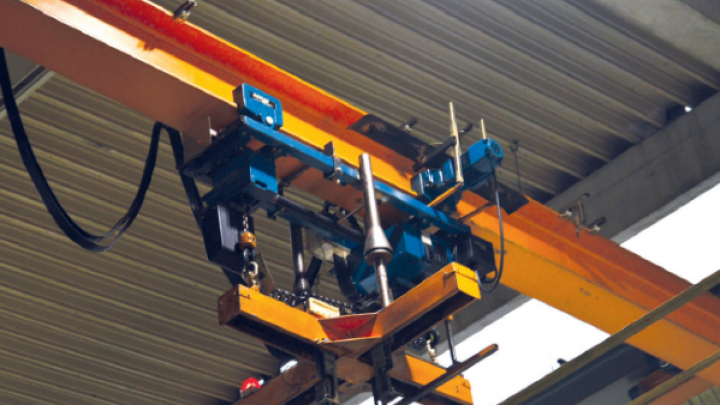
Unutrašnja logistika, odnosno tok materijala u okviru fabrike, predstavlja srž svakog proizvodnog sistema. Dugoročni trend je da se tokovi materijala automatizuju, u što je moguće većoj meri.
U zavisnosti od tipova procesa, automatizacija tokova materijala može da bude delimična, kod poluautomatskih procesa, odnosno potpuna, kod potpuno automatizovanih procesa.
Projektni zadatak koji je poveren inženjerskom timu Tecon sistema, pod vođstvom dr inž. Zorana Petrovića od strane Trelleborga, kao investitora, odnosno Termoinženjeringa, kao glavnog izvođača izgradnje novog pogona, obuhvatao je projektovanje dva specijalna krana koja se nalaze na istoj kranskoj stazi, čija je uloga delimična automatizacija proizvodnog procesa vulkanizacije guma za poljoprivrednu mehanizaciju.
Proces nije bilo moguće u potpunosti automatizovati iz dva razloga. Prvi je dopremanje sirovih guma, koje se vrši viljuškarima, nakon čega se gume prihvataju specijalnom obrtnom, prihvatnom rukom, što se radi u ručnom radnom režimu. Drugi razlog je zahvatanje vulkanizovanih guma, koje se vrši preko specijalnog zahvatnog uređaja, kako bi se obezbedilo zabravljivanje gume i sigurna manipulacija.
Taj deo proizvodnog procesa mora da se odvija u ručnom radnom režimu, u kojem operater upravlja kranom, odnosno zahvatnim uređajem.
Prese za vulkanizaciju guma se nalaze raspoređene sa jedne i druge strane proizvodne hale. U sredini, između presa, postavljen je konvejer, koji služi za transport vulkanizovanih guma do odeljenja za kontrolu kvaliteta (Slika 1).
Sirove gume se dopremaju do svake prese posebno, pozicioniraju na presu i nakon njenog zatvaranja, počinje proces vulkanizacije. U zavisnosti od tipa gume, proces vulkanizacije može da traje od jednog do nekoliko časova.
Kompletan proces vulkanizacije, kontrolisan je preko centralnog PLC-a, koji je povezan sa PLC-om koji se nalazi na svakoj presi i kontroliše njen rad.
Staro rešenje je podrazumevalo da se nakon završetka procesa vulkanizacije, gume manuelno transportuju do odeljenja za kontrolu kvaliteta, nakon čega se odlažu u magacin gotovih proizvoda, pod uslovom da zadovolje kontrolu kvaliteta.
Ukoliko ne zadovolje, odlaze na doradu u slučaju da je ona moguća, odnosno ukoliko nije, deklarišu kao škart i tretiraju kao proizvodni otpad.
U cilju automatizacije ovog procesa, osmišljeno je tehničko rešenje sa dva poluautomatska krana, kako bi se obezbedio optimalni proizvodni ciklus.
Svaki kran ima ukupnu nosivost od 1,25 t, a opremljen je sa po dva specijalna lančana vitla, nosivosti po 0,63 t. Prihvat guma je putem specijalnog automatskog zahvatnog uređaja, koji se veša na kuke lančanih dizalica.
Kako bi se obezbedila simultanost u radu oba vitla, pribegnuto je specijalnom rešenju, kod kojeg su dve lančane dizalice spregnute, mehanički, preko torzione osovine.
Na ovaj način je, krutom vezom, omogućeno potpuno simultano kretanje kuka oba vitla. U toku projektovanja, urađena je kompletna statička i dinamička simulacija rada specijalnih kranova sa zahvatnim uređajima, kako bi se ispitalo njihovo ponašanje u toku eksploatacije (Slike 2 i 3).
Na osnovu svih dobijenih parametara od strane investitora, pokrenut je inovacioni projekat razvoja prototipnog zahvatnog uređaja za prihvat vulkanizovanih guma različitog prečnika.
Zahvatni uređaj se sastoji od čelične konstrukcije, kinematskog mehanizma za pomeranje čeljusti, odgovarajućeg motora sa reduktorom, kao i sistema senzora koji obeezbeđuju informacije da je alat dobro pozicioniran na gumi, odnosno da je guma dobro zahvaćena čeljustima i da može da se bezbedno odloži na konvejer.
Nakon statičkog i dinamičkog testiranja konstrukcije zahvatnog uređaja, odnosno funkcionalnih testova kompletne grabilice bez i sa opterećenja, zahvatni uređaj je integrisan u kranove (Slika 4).
Sistem se već nalazi u fazi stabilne eksploatacije, koriguju se određeni elementi njegovog rada, kako bi se dobili optimalni parametri radnog ciklusa (Slika 5).
Već se razmišlja i o unapređenju sistema, tako da se razvija kompletan modul, u skladu sa inicijativom Industrija 4.0, kako bi se što je moguće efikasnije ispratio rad sistema.
Modul podrazumeva praćenje parametara rada sistema preko interneta, tako da će svi tehnički podaci biti dostupni u realnom vremenu.
Takođe, razvija se i specijalni HMI interfejs, koji će biti baziran na Android platformi i koji treba da omogući jednostavnije i ergonomičnije upravljanje sistemom od strane rukovaoca.
Očekivano vreme za primenu unapređenja je druga polovina ove godine.
Posebnu zahvalnost, inženjerski tim Tecon sistema duguje kolegama iz Termoinženjeringa, koje su učestvovale na razvoju ovog, prototipskog, rešenja, kao i kolegama iz Trelleborga (pre svih g-dinu Aligeru, koji je podržao ovaj pionirski poduhvat, g-dinu Mikulki koji je upravljao projektom razvoja sistema i g-dinu Radišiću, koji je zajedno sa inženjerima Tecon-a učestvovao u razvoju sistema).
Detaljnije informacije na:
TECON Sistem d.o.o.
Antifašističke borbe 21 b
11070 N. Beograd, Srbija
tel/fax: + 381 11 301 78 74, 311 66 50
e-mail: office@tecon.rs
www.tecon.rs