ENGEL presents new injection units at K 2016 - New ENGEL victory and ENGEL duo for even more precision, ergonomics and efficiency
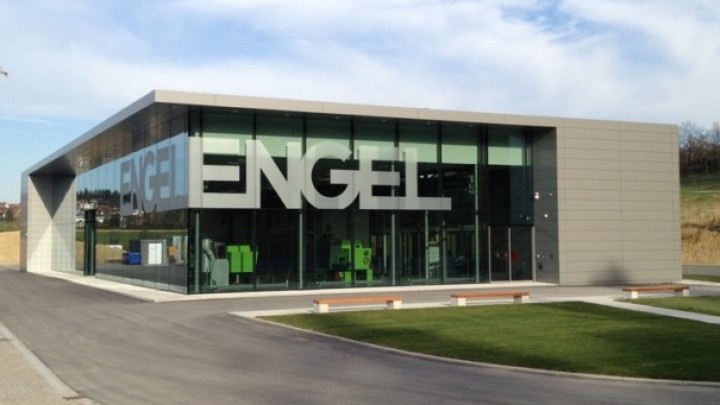
ENGEL AUSTRIA has revised its hydraulic injection units from scratch and will present the next generation of its successful ENGEL victory and ENGEL duo series of injection moulding machines at the K 2016 trade fair in Düsseldorf, Germany, from October 19th to 26th. With their innovative features, the machines achieve even higher levels of precision, ergonomics and efficiency than before.
Together with the clamping unit, the injection units form the heart of every injection moulding machine. These two central elements are responsible for the performance of the machine and decide on its efficiency. ENGEL will present the result of its long development work on the hydraulic injection units at the K 2016.
Even more precise injection
Based on its many years of experience in the different fields of use of its injection moulding machines, ENGEL has restructured the sizes of the units and optimised their performance data, such as injection pressure, injection speed and plasticising capacity, for current and future requirements. As a result it will be possible from now on to accommodate the individual wishes of users more specifically when designing the machine. All in all, the new units enable more precise injection and higher process stability.
Control of temperature and pressure in the barrel contribute to this in equal measure. Special attention was paid in development to temperature control of the feed throat. The temperature control range was enlarged to safely rule out clumping in the feed zone and absorption of moisture across a wider range of materials. The new concept minimises energy losses both during heating and cooling of the feed throat. The main contributor to better controllability of the pressures is the revised piston design.
To achieve high process stability even when ambient conditions and raw materials fluctuate, ENGEL has developed its iQ weight control software to detect such variations and to compensate for them automatically within the same shot. This solution has established itself well in injection moulding machines with electric injection units. As from K 2016, the software will also be offered as option for hydraulic injection moulding machines.
Even faster barrel changes
The new design features of the hydraulic ENGEL injection moulding machines moreover improve ergonomics, both for the machine operator as well as the maintenance technician. The new arrangement of the control cabinets and pumps of the ENGEL duo injection moulding machines has improved clarity of the layout and accessibility. In some machine models the footprint has even been reduced.
The new covers now consist of two parts and are equipped with integrated handles. They are very quick to open, which saves time, for example, when servicing the pumps.
When replacing barrels, the dismounted barrel can from now on be put down outside the machine without any need for additional equipment. The barrels are equipped across the board with stable pedestals. No special tools are needed to mount or dismount the barrels, which speeds up the process and reduces downtimes.
Efficiency has been improved considerably in the large units as only a few screws now need to be loosened and tightened again when replacing them. With the new design, ENGEL has applied the principle of quick mould clamping to the barrel.
Even more energy savings
In addition to the new feed throat temperature control, another strong contributor to the energy efficiency of ENGEL victory and ENGEL duo machines is ecodrive. The ENGEL servohydraulics, proven in many years of use, belong to the standard equipment of the new machine models. The key to high energy efficiency here lies in needs-related pump output.
If the machine is at a standstill, for example during cooling, the motors are also idle and do not use energy. The positive side effects of this are that the machines run much more quietly and that the hydraulic oil does not heat up as much, which also reduces the workload on oil cooling.
K 2016 sounds the starting point
ENGEL will present the hydraulic injection moulding machines in new design for the first time at K 2016, where it will dedicate a separate Expert Corner to the injection units. To begin with, the ENGEL victory machines from an injection unit size of 860 (screw diameter from 45 to 55 mm) and the ENGEL duo machines to size 23060 (screw diameter from 135 to 170 mm) will be available for order in the new design. The other sizes will follow successively after the fair.
The ENGEL victory and ENGEL duo injection moulding machines both belong to the most-sold ENGEL injection moulding machines worldwide. The ENGEL victory covers a wide spectrum of applications. Due to its tie-bar-less clamping unit, it enables especially efficient manufacturing concepts in highly integrated and automated processes as well as in multi-component applications. The series covers clamping forces from 280 to 5,000 kN. Thanks to their two-platen construction, the
ENGEL duo large-size machines with clamping forces from 3,500 to 55,000 kN combine very high efficiency with a comparably small footprint for the manufacture of large components.
ENGEL at K 2016: hall 15, stand C58